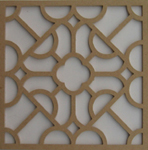 |
Profile machining
Profile Machining is widely used for incising. It includes On Line, Outside, and Inside machining.
|
 |
Ramp
Ramp is to plunge in a certain angle. Tools goes into the material not in a vertical direction but in slanting direction so that the tool will not be destroyed or broken because of force during entering material. This also ensures that no mark or scar be left on the surface of the material.
|
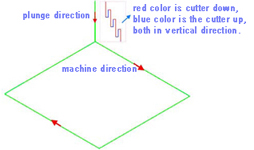 |
Pecking plunge
When using Pecking plunge, the tool goes into a certain depth into the material, and then goes up to a certain height, and repeat this process when cutting the material. Pecking plunge prevents the tool breaks especially when cutting hard materials.
|
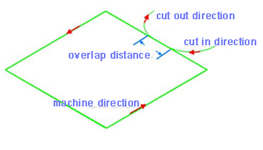 |
Lead in/out
When using Lead in/out, the tool first goes into a certain depth outside of material, and then cuts into the side of the material. |
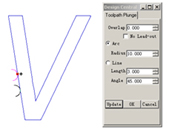 |
Toolpath plunge
You can modify the start point of profile path by click the start point, and keep the left mouse key down, drag the mouse to move the start point. And the same time the plunge will be modified by the parameter of dialog. |
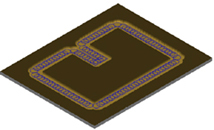 |
Trochoidal toolpath in profile machining
The Trochoidal Toolpath is designed especially for brittle materials such as glass or granite or extremely hard materials that generate a lot of heat upon cutting. The Trochoidal Toolpath produce a circular toolpath at high feed rates with low load on the tool, therefore keeping the heat down while providing for longer tool life. |
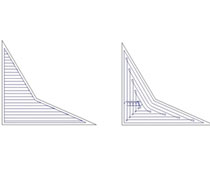 |
Area Clearance
Area Clearance is to mill an area in the material. There are two types of milling: raster and offset. It is commonly used in our work.Offset (a machinery strategy of Area clearance) has changed the line-transition into arc-transition and the arc buffer has been added as a transition for sharp corners to adjust to high-speed milling.
|
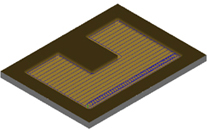 |
Trochoidal Slot in area clearance
Trochoidal toolpaths are mostly used to create slots in double side cutting. You can use trochoidal paths to create pockets, but there will be some wasted movement when the pocket opens up, and the arcing paths are unnecessary to minimize engagement. |
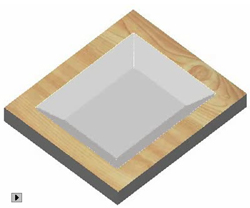 |
3D Corner Engraving
3D Corner Engraving is to make the surface of the material smooth and to ensure the definition, precision and 3d effect of the machined object. It is mainly used in seal engraving and engraving of characters with special effects. 3D Corner Engraving includes top and bottom engraving, and the difference between them is the size of the machining area. |
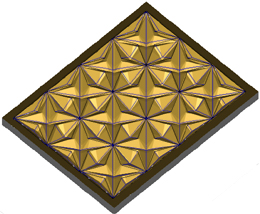 |
Midline Machining
Midline machining is to machine along the middle axis of the drawing. |
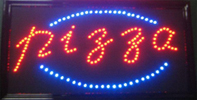 |
Drilling
You can Drilling on points, on curves, on the center of object
or in region. |
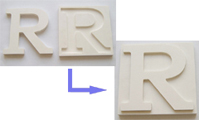 |
Insert and Inlay
This is a special function of engraving. It is an important measure to make sign marks and craftworks. |
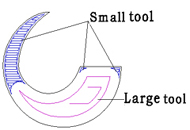 |
Intelligent machining
Efficiency in milling can be greatly improved when applying Intelligent Machining. Two different tools can be chosen from the toolpath, the tool with lager diameter will be used for rough machining, and the smaller one will be used for precision machining. In the first machining, the speed is greatly improved, and after the second process, you will get what you want. |
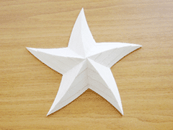 |
Prism machining
By prism machining, it becomes easier for you to make characters with prism effect, and sign mark. Toolpaths can be created quickly and efficiently. If you want to make a massive work, it can be machined layer by layer, and you can fit them together when finished. There are two kinds of angles for you to choose, rounded angle and cusp angle. The prism will display clearly. Prism machining is quick to learn and easy to use. |
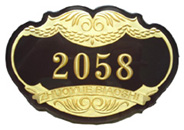 |
Embossing machining
Embossing machining is mainly used in making relief. There are two modes in embossing: concave relief machining and convex relief machining. With ease operation, you will get accurate relief. It is widely used in such fields as advertising sign, sign board, breast card, furniture, metallic moulds, printings, etc. |
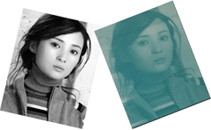 |
Image dot machining
Image dot machining is to engrave the object after the image is converted into grayscale image. Dots are made on the material based on the different grayscale value. The higher the grayscale value is, the deeper and bigger the dots are, and vice versa. |
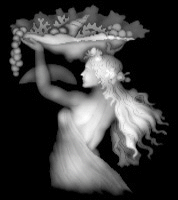 |
Image relief machining
Image relief machining is to engrave the object after the image is converted into grayscale image. The machining is based on brightness level. Min brightness depth and max brightness depth are the depth by which the tool goes into the material. Horizontal/vertical machining is the direction of the tool path. |
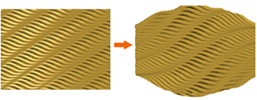 |
Toolpath artistic transform
Perspective Distortion and Envelop Distortion can support the toolpath transform. especially can be applyed to the waveboard toolpath. |
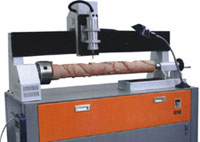 |
Rotary_Axis engraving
This is used to drive a machine using rotary axis, do cylinder engraving. |
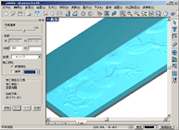 |
Toolpath simulation
Machining process can be previewed through toolpath simulation, thus avoiding trial cutting and reducing cost. This function is helpful for choosing a proper machining type. |
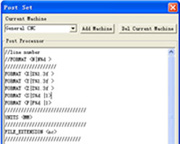 |
Post Processor
The Post Processor is a programme which converts the tool path in some standard neutral format into the format requried by a specific machine control system. Such as Biesse, CAMtech, Fanuc, Homag, MasterWood, Microstep, NcStudio, RichAuto, SYNTEC, SCM, etc..
|